- Home
- Case Studies
- Tata Chemicals
Company
Tata Chemical Europe (TCE)
Commissioning Commenced
2021
Application
Carbon Capture and Utilization
Capacity
- Capturing 40,000 TE of CO2 A Year
- Resulting in 10% carbon reduction
Benefits
Reduced the carbon emissions from Tata Chemicals Europe operations by approximately 10%. This results in capturing 40,000 TE of carbon dioxide per year.
Location
United Kingdom
TCE INVESTS IN UNITED KINGDOM’S FIRST CARBON CAPTURE AND UTILIZATION PROJECT
How can we reduce our carbon emissions? How can we lower carbon dioxide (CO2) emissions and improve utilization of our own value stream? These are questions many industries and companies ask themselves, especially as taxes for emitting CO2 inevitably trend upward. Tata Chemicals Europe (TCE) has taken a leading role in the United Kingdom by investing in a Carbon Capture Utilization (CCU) plant that will capture their combined heat and power (CHP) plant’s CO2 and use it in their production of sodium bicarbonate.
TCE appointed Pentair to handle this exciting carbon capture utilization initiative, which will open in the second quarter of 2022. TCE CCU Project Manager Stewart Prentice stated, “The project could help pave the way for other industrial applications of carbon dioxide capture and is an important step in decarbonizing industrial activity.”
The captured carbon dioxide will not only reduce TCE’s carbon emissions but will also be used to make sodium bicarbonate to be known as EcoKarb®. Carbon dioxide is a key ingredient in high-grade sodium bicarbonate, which is most often used in the pharmaceutical sector and for hemodialysis, a type of treatment for kidney failure.
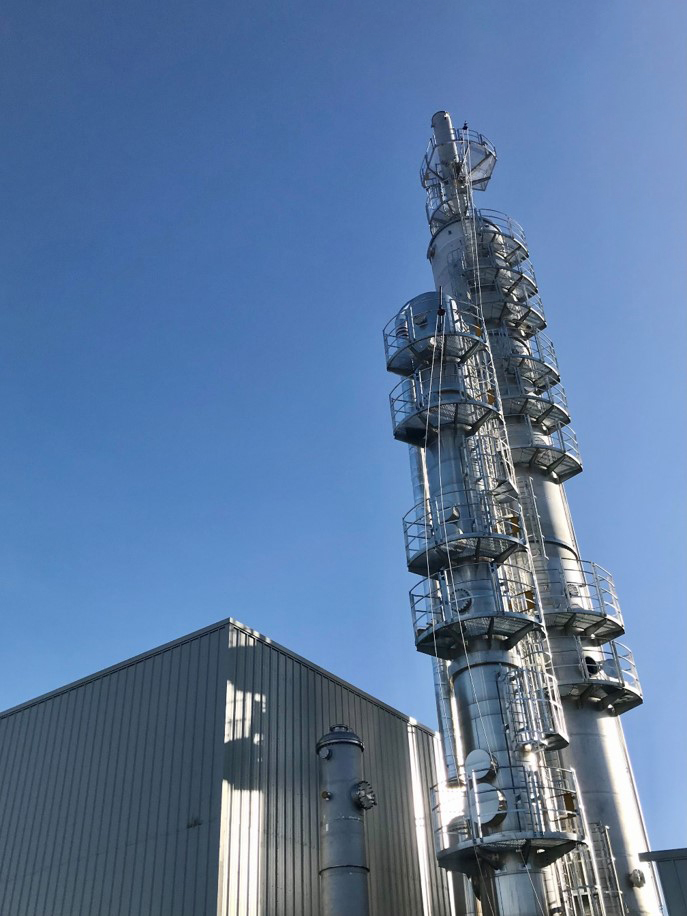
INNOVATIVE AND WELL-PROVEN APPLICATION OF CARBON CAPTURE UTILIZATION TECHNOLOGY
In an innovative application of CCU Technology, the TCE plant will capture carbon dioxide from the flue gasses of TCE’s gas-fired 400 MW steam combined heat and power (CHP) plant, which supplies steam and electricity to the company’s Northwich, England, operations and other industrial businesses in the area.
The CCU plant extracts, purifies and liquefies the CO2 contained in the flue gas for use in the manufacture of sodium bicarbonate. Deploying CCU technology will reduce emissions as the captured CO2 is utilized in the manufacturing process versus being emitted into the atmosphere. CCU is based on Pentair Advanced Amine Technology (AAT).
ADVANCED AMINE TECHNOLOGY IS BOTH ROBUST AND FLEXIBLE
Pentair AAT is an industry-leading technology to capture carbon dioxide from any flue gas, including non-power generation sources such as limekilns. The process is designed for gas streams having low partial CO2 pressure, as is the case for flue gasses.
The design philosophy when creating an efficient CO2plant is crucial in obtaining a robust and flexible process. In-depth knowledge of butterfly effects of various process instabilities and offsets helps to ensure proper process control and a well-trimmed plant, which is key for helping ensure continued high CO2 quality.
Initially, AAT technology was designed to meet the very strict quality needs put forth by the global food industry and the merchant gas market, but has now found its way to large industrial manufacturing companies using CO2 as source material, requiring the same food-grade quality as food industry producers.
To support these significant industries, the technology is further developed to offer large-scale CCU and Carbon Capture Sequestration (CCS) projects.
Pentair has extensive experience and a deep understanding of amine technology, having installed more than 300 amine plants globally.
“We worked closely with Pentair to develop a unique solution to capture carbon dioxide emissions that are then recycled to produce sodium bicarbonate. The official opening of the plant celebrates a major milestone in Tata Chemicals Europe’s journey to reducing carbon emissions from our operations with the carbon capture plant reducing our emissions by approximately 10% at our CHP plant. The solution we have created with Pentair demonstrates that innovation and technology can meet industrial challenges like our own.”
- Martin Ashcroft Managing Director Tata Chemicals Europe
PENTAIR NOXFLASH ELIMINATES THE NEED FOR POTASSIUM PERMANGANATE
During the CO2 capturing process, certain impurities like NOx need to be efficiently eliminated. Patented Pentair NOxFlash Technology helps to remove the risk of contaminating the liquid CO2 with NOx. This approach provides an efficient alternative to the traditional method of removing NOx from the CO2 that entails scrubbing the gas with a potassium permanganate (PPM) solution. PPM is a strong oxidizing chemical that requires caution in handling of both the initial chemical solution and its waste by-products. Use of such substances could create additional plant resource burdens as they may entail more considerations such as worker safety due to exposure precautions, environmental concerns due to disposal procedures and other costs such as supply due to more regulated import/export. By avoiding the use of PPM in the process, plants may avoid these issues, thereby alleviating these potential costs and other resource factors.
Among other advantages, Pentair NOxFlash, in combination with the distillation column, also optimizes the process to yield better food-grade quality CO2. The resulting product is a CO2 liquid at approximately 18 barg and -25° C with a purity of more than 99.999% (according to European Industrial Gases Association (EIGA) specifications2 ), ready to be used as pharmaceutical grade sodium bicarbonate, as requested by TCE.
Pentair has installed more than 2,000 CO2 plants globally meeting these specifications.
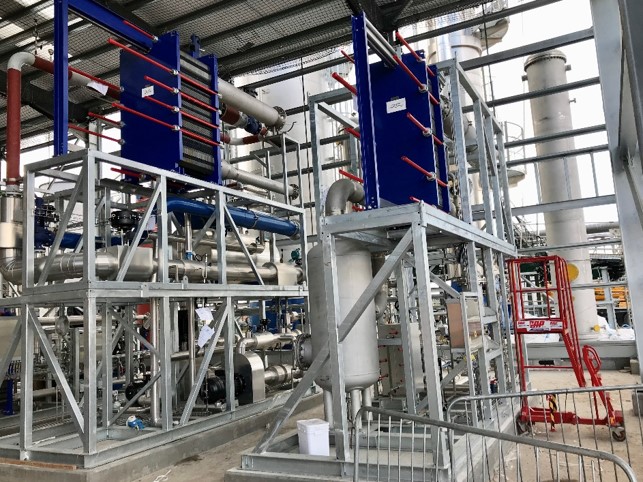
ATTRACTIVE FOR MULTIPLE INDUSTRIES
The CCU plant will see TCE taking a leading role in helping prove that this technology can help the UK reach its net-zero goal in reducing 100% of greenhouse gas emissions by 2050 and ensuring ongoing emissions are balanced3.
According to TCE, the project is expected to be a springboard for TCE to help unlock further growth into their export markets. Examples like these can be an important source of inspiration for other industries, irrespective of the ability to utilize the captured CO2 internally or the option to sell to third parties. Another potential option is sequestration of the capture CO2, where the business case is strongly related to storage options.
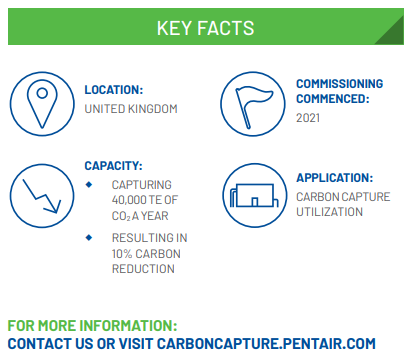
[1] “The Ten Point Plan for a Green Industrial Revolution”, HM Government, date accessed 24th May 2022, date published November 2020, Pg. 23 Read More
[2] The Pentair Carbon Capture plant installed at Tata Chemicals Europe Northwich, UK site is designed to process 115 tons of carbon dioxide per day.
The equivalent number of cars is calculated using:
- The average CO2 emissions per kilometre of new cars registered in the UK since 2015:”New Car Carbon Dioxide Emissions, DfT Business Plan”, Department for Transport, Gov.UK, data accessed 15th June 2022, Date Published 12 December 2013, Last Updated 15th July 2015, Read More.
- The average distance travelled per car per year in the UK in 2018 using data from the UK Department of Transport: nts0901.ods (live.com) Last accessed 15th June 2022. 2018 as base year as 2019-2021 data is affected by the COVID-19 pandemic that would potentially overstate the equivalent number of cars taken off the road in the UK as each car travelled fewer kilometres in this period.
[3] “Climate change targets: the road to net zero?”, UK Parliament, House of Lords Library, date accessed 9th June, 2022, date published 24th May, 2021, Read More.
[4] “Minimum Specifications for Food Gas Applications”, European Industrial Gases Association, date accessed 20th June 2022, published 2020, Pp. 2 & 4, Read More.
Title | Download PDF | |
Brochure | Tata Chemicals Europe | Download |
Related Products
The NOxFlash replaces the traditional use of scrubbing with Potassium Permanganate (PPM) in your CO2 production plant. Ideal solution – unaffected by variations - in fuel composition or combustion that is out of specification.
Pentair CO2 Self-generating Plants - Combustion Based Unit - CBU
Based on the latest technologies, CO2 generating plants (CBU) from Pentair meet the strictest CO2 quality requirements.
NEWS